SHARE
in social networks
Paint for concrete floor helps protect the surface from wear and damage that can occur during operation. Even with the narrow purpose on the market range of compositions can knock a buyer confused. This article will help you understand the features of protective coatings for concrete surfaces, as well as choose the best option paint for interior and exterior applications.
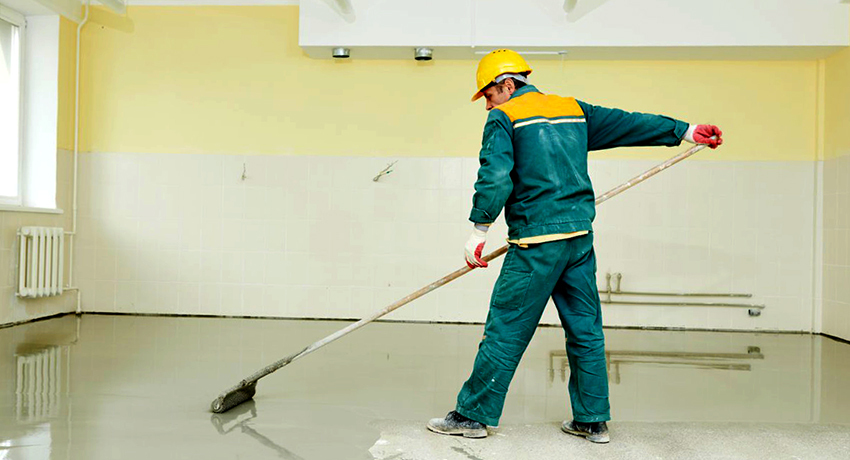
Painting concrete floor to protect it from damage and rapid wear
Content
-
1 The coated concrete floors, and why it may be necessary
- 1.1 Specificity of paints for concrete floors in the garage
- 1.2 The paint concrete floors on the street: the compositions for external works
- 2 Advantages of painting the concrete floor: the feasibility of the procedure
-
3 The paint concrete floors: the main types of compositions
- 3.1 Characteristics of acrylic paints for concrete floors
- 3.2 Especially acrylic-silicone wear-resistant floor paint
- 3.3 Advantages of epoxy paints for concrete floors
- 3.4 Characteristics of urethane alkyd based paints
- 3.5 Specificity of rubber paint for concrete floors
- 3.6 Advantages of polyurethane paints for concrete floors
- 3.7 How to paint the floor of concrete: a primer for an alternative budget
-
4 Review of the best colors for the floors made of concrete from popular and trusted manufacturers
- 4.1 Overview epoxy paint for concrete floors "Epostoun"
- 4.2 Overview polymer paint characteristics for the "Tex" floors
- 4.3 Paint for concrete floor "Teksipol" acrylic-based
- 4.4 Benefits "Betoksil" acrylic paint for concrete
-
5 How to paint the floors of concrete: Preparing the base and application technology
- 5.1 How to paint the concrete: The technology of drawing a two-component composition
The coated concrete floors, and why it may be necessary
Concrete is widely used in construction. This material is suitable not only for the creation of foundations and walls, but also for the manufacture of floors. Concrete is used in residential areas, as well as storage, industrial and technical use.

Concrete paints are for interior decoration or exterior
Subject technology base obtained strong and durable. However, this material is not without drawbacks. Not having the protective layer, its surface is subjected to abrasion, as well as the damaging effects of negative factors. Therefore, the question inevitably arises about what color the concrete, to prolong its service life. When choosing the protective composition is primarily operating conditions should be taken into account.
Depending on the conditions under which will be operated by the treated surface, paint divided:
- on coatings for interior applications;
- compositions for exterior finishes.
Each group of the dyes has the features and characteristics that enable to use these materials in certain circumstances.
Specificity of paints for concrete floors in the garage
Concrete base - one of the most reliable and affordable coverage options, so the tie is often used to create floors in the garage. But do not forget that such a surface is constantly exposed to mechanical stress, and corrosive substances. In addition, during the operation on it accumulates cement dust.

For painting the garage not suitable alkyd, oil and organic fluorine compounds
Similar problems will help to cope properly matched paint. Because it will be used indoors, such coatings are special requirements. Paint for floors in the garage should be:
- durable;
- without smell;
- flame retardant;
- resistant to chemicals;
- fast drying;
- washable;
- weatherproof.
Unfortunately, there is no universal formulation that would fully meet all of these requirements. Therefore, the paint is chosen based on the operating conditions of the room.
Important! Choosing what color the concrete floor in the garage, you should avoid the fluoro-organic dyes, as well as compositions of alkyd and oil-based. After contact with petroleum fuels and lubricants for such coatings changing their chemical composition and reaction occurs.

Paint the garage must be washable, fire-resistant, wear-resistant
The paint concrete floors on the street: the compositions for external works
Normally, concrete is used in open spaces, so some consumers do not see the need to use floor paint for exterior use. They believe that having high strength and excellent technical characteristics of this material needs no additional protection and can be used successfully in almost any conditions. In fact it is not. Located outdoors exposed concrete surface ravages of such negative factors:
- precipitation and wind;
- low and high temperatures and their differences;
- ultraviolet radiation;
- industrial gases.
The concrete screed has a high porosity, so the material absorbs moisture, which can fall on its surface in the form of rain or accidentally spilled liquids, as well as just come from atmosphere. Without quality of the protective coating is all will remain and accumulate inside the base, which is critical for its condition. Especially if the surface oil or dirt enters, for example, antifreeze, gasoline, or oil.
Concrete surfaces outdoor subjected to impact loads, abrasion and impact abrasives. In such circumstances, the access portions are operated, the parking designed for trucks and the trestle. Not having the appropriate protection coupler quickly lose its attractive appearance and become unusable. On the concrete will be chipped, cracks, breaks and potholes. It is therefore very important to choose the right protection for the surface composition.

Suitable for outdoor use special paints for concrete, impregnation and resin enamel
How to paint the concrete on the street? For this purpose, these types of coatings are applied:
- Impregnation - means penetrates through the pores of the material thickness of 7-10 mm and solidifies, preventing the ingress of dirt and fluid. After treatment the concrete surface becomes firmer. Such a base can tolerate moderate load. only a limited service life refers to the disadvantage of impregnation.
- Polymer enamel - deemed optimal for this protection. This category includes coating compositions containing epoxy resins, acrylic or polyurethane.
- Specialized varnish for concrete floors - made on the basis of aqueous dispersion and comprises latex components. Means, used for insulation of concrete screeds.
Note!Experts do not recommend the use of varnished concrete structures for protection, because they are not able to create a coating of sufficient strength.
Advantages of painting the concrete floor: the feasibility of the procedure
Concrete is a conglomerate. It includes a number of elements which have different physical state and chemical composition. This explains its porous structure, which also includes solid components. Some tiny pores sized cement filled gelled substance having a viscous consistency. The remaining capillaries and cavities contain air or water, which upon hydration remained unbound or just got there from outside.

Painted concrete floors is not dusty, and it becomes more strong and durable
Such structure of the material is favorable for erosion. This process is particularly active in the areas where the screed is subjected to mechanical stresses, to aggressive chemicals and adverse environmental factors. It is in these conditions maintained concrete floors in garages, workshops, technical facilities and household goods.
Without sexual paint concrete base quickly comes to the unsuitability of:
- reduced strength characteristics;
- strongly dusty surface;
- cavities and cracks appear;
- coating crumbles;
- some parts become unstable.
Sexual paints for concrete floors have a good penetrating ability. Entering into the structure of the material, they are "sealed" void preventing ingress of moisture and reactive materials. After staining screed surface is formed a thin film. Due to its durability it protects floors from premature wear.
Advantages of concrete painting:

Without painting a concrete floor very quickly comes unusable
- Improved surface such factors as strength and resistance to wear.
- Completely eliminates the possibility of dusting.
- On the surface formed waterproofing coating that protects floors from moisture, chemically active substances, and oil products.
- Prolongs service life of the concrete base.
- It becomes possible to reduce the overall estimates through the use of cement slurries of lower grade without degrading the performance of the coating.
- It simplifies the process of care for the flooring.
- Paint colors varied enough for the floor, which improves the fine quality of the concrete screed, and to create a beautiful design.
Note!Any paint will have from time to time to update. However, the cost of such measures is considerably less than a deep restoration of the concrete floor, or it perezalivke.
The paint concrete floors: the main types of compositions
Paint for concrete protection, should have certain properties. If you wish to get really high-quality coating will not be able simply to restrict cheap oil composition. He will not be able to provide surface durability and protection at an appropriate level. Its use is, on the contrary, may provoke a more rapid degradation of the material.
For these purposes it is better to use a polymer paint for concrete floors:
- acrylic;
- rubber;
- urethane;
- epoxy;
- polyurethane.

For painting concrete floor suitable for a variety of polymeric compositions
Each type of structure has certain characteristics, advantages and disadvantages, as well as special operating conditions. All these details must be considered when choosing a dye for floors.
Characteristics of acrylic paints for concrete floors
For the production of dyes of this type are used acrylic resins, pigments and organic and inorganic origin. They are made on the basis of polyacrylates and acrylates in combination with components that form a protective coating. The composition may also be present esters provide quick drying and resistance to the influence of moisture.
Many manufacturers claim that the qualitative result only one application is sufficient. However, in practice, still need at least two layers. Consumption acrylic dyes is about 0.1-0.2 l / m². These compounds are ideal for the treatment of a small area of space.
The main application of acrylic paints for floors:
- garages;
- basements;
- balconies.

Acrylic paints are suitable for floors on balconies, garages and basements
Compositions based on acrylic are resistant to short exposures of non-corrosive chemicals and moisture. On sale you can find a variety of colors and shades. With acrylic dyes obtained as matte and glossy finish. In the role of the solvent acts as ordinary water. This version of dyes is one of the most affordable. Acrylic compounds are the materials category, odorless and fast drying floor paint. They dry out after about 12 hours. Walk freely on such a coating can be within 48 hours.
The advantages of acrylic-based inks:
- environmental friendliness;
- security;
- resistance to moisture;
- increase of strength characteristics of the treated surface;
- resistance to high temperatures;
- durability.
Useful advice!Acrylic paints are best used on the second floor, if available, or in a dry basement. It is not recommended to use them as the primary coating.
Especially acrylic-silicone wear-resistant floor paint
These products are made of silicone resin and acrylic copolymers. Acrylic-silicone enamels belong to the category of wear-resistant formulations. This type of two-component paint for concrete floor combines all the advantages of silicones, and acrylics. These elements form a coating with a specific structure having a high strength and resistance to various mechanical loads. In addition, the acrylic-silicone enamel do not have favorable conditions for the development of harmful bacteria.

Acrylic-silicone paints are characterized by high resistance to wear
Acrylic resins have excellent adhesion properties, so paint is well retained on a concrete base. When the coating sufficiently elastic. Such property is ensured by the presence in the silicone resin. They are substances polymeric origin. Due to the silicon coating is quite durable. Silicone resins are another useful quality - electrical charge. Due to this property, the surface repels dust.
Silicone-Acrylic enamels have many advantages and only one drawback. The color range of these dyes is very limited. The composition is applied to the concrete surface at least two layers. Before re-staining, it is necessary to wait until the first layer dries. This requires at least 3 hours.
Related article:
Repair concrete floor: features of the process of restoration and complete replacement of the screed
Classification and mixtures choice. Features the work. The cost of repairs. Recommended composition.
Advantages of epoxy paints for concrete floors
Epoxy formulations for concrete surfaces are bicomponent dyes that must be mixed before use. It should be done very carefully to get a homogeneous mass. The water may be used as the solvent. The color scheme of epoxy compounds is small, however, compared to the numerous advantages of the wear-resistant paint for concrete floors, this shortcoming can not be taken into account.
Epoxy enamels possess high resistance to abrasion and wear. After drying the paint and is transformed into a durable tough coating, so it can be used even for treatment of floors in industrial environments. Epoxy mixture can withstand high mechanical loads. They are not afraid of the negative impact of different weather conditions, therefore suitable for use outdoors.

Epoxy paints are resistant to changes in temperature
Advantages of epoxy floor paint:
- high levels of resistance to the effects of moisture;
- excellent adhesion properties (with prior degreasing the surface);
- high degree of protection from exposure to various chemicals (alkalis, acids, oils, saline solutions);
- color to be persistent for a long time, does not burn and does not undergo changes.
Note!Epoxy dyes are applied in at least two layers with an interval not less than 12 hours.
Characteristics of urethane alkyd based paints
These paints are made on basis of alkyd resins. The compositions have a high hiding power. To obtain a good result floors are processed at least twice. Between the application of the first and second layers must pass day. That's how much time is required to complete the drying. After 24 hours after the last layer, the flooring can be commissioned has been applied. However, the coating is fully cured only one week later.

Urethane paint necessary to cover the floor in at least two layers
As polyurethane paint, floor enamel based on alkyd exhibits high abrasion resistance. Concrete substrates treated in such a composition, can be operated for a long time (up to 15 years). Before using a urethane paint must be diluted. To do this, use mineral spirits. With it, is 10 percent solution. spray gun can be used for applying the dye.
The sale can be found urethane compounds for interior and exterior use. The choice of colors is quite extensive, but great demand yellow, golden, gray and brown floor paint. After drying, the coating becomes glossy. Some users consider this feature urethane dyes as a significant drawback.
Specificity of rubber paint for concrete floors
Rubber compounds are ideal for coloring floors in the garage. These compositions have unique properties and characteristics. The main advantage of fast drying paint rubber flooring is that the coating hardens after 30 minutes after application, provided that the indoor temperature is not lower than 20 ° C. This does not mean that the staining can not be produced at low temperatures. Floors can handle and when the mark on the thermometer reaches -30 ° C. In such circumstances, of course, the dye will dry longer.
According to its properties resemble rubber compounds, polyurethane paint, as they have a similar composition. This coating may be operated in a wide temperature range (from -50 to +60 ° C), which allows the use of a composition for staining floors in unheated rooms.

Rubber paint for concrete floors are the most quick-drying
The advantages of rubber paint for floors also include a long service life. This coating retains its properties for 10 years. The maximum flow rate of the dye is 400 g / m². The composition may be applied by roller or brush. In rubber compounds it has only one significant drawback - their high cost.
Useful advice! To get a budget option for protective coating for concrete floors in the garage can be treated with the help of polyurethane or epoxy primer.
Advantages of polyurethane paints for concrete floors
Polyurethane enamel are one- and two-component. If you intend to treatment of concrete floors in the garage, it is desirable to give preference to the second option. Such formulations are suitable for interior and exterior work. Before using a two-component polyurethane paint for the floor it is necessary to mix. It should be done very carefully to remove any bubbles, as well as to eliminate the likelihood of clots.
For complete drying of the coating takes about 2 weeks, this process takes place in several stages:
- moisture evaporates;
- material solidifies;
- Floor gradually gaining mechanical resistance.

The polyurethane mixtures are suitable for both external and internal works
Once all steps completed drying, coating is durable and resistant to aggressive chemicals.
Advantages of concrete polyurethane polymer paint:
- The coating may be used in extreme weather conditions (paint feels great in the temperature range from -60 to +80 ° C).
- Affordable.
- Resistance to mechanical stress.
- Economical consumption.
- Wear resistance.
- for chemical resistance.
The disadvantages are just too "moodiness" composition. Staining can produce only in the case when the room temperature at least 5 ° C, and the humidity does not exceed 75%. If you ignore these requirements, covering not just "grab".
How to paint the floor of concrete: a primer for an alternative budget
Before any concrete type dyeing dye previously prepare the surface needed. This typically use a primer solution. This rough layer is necessary in order to improve the adhesive properties of the paint material and provide good coupling with the concrete surface.

Polyurethane primer well aligns floor and fills the void
Some species composition of the soil can be used as separate materials for dedusting surface. When finishing floors in the garage decorative component is usually a secondary role, however such a solution may be the best option.
Note! As an independent materials for dust removal of the concrete surface can be used, not all kinds of primers. For these purposes, intended only polyurethane and epoxy compounds.
Advantages of polyurethane primer:
- composition well fills all voids in the concrete lining surface and increasing its strength;
- excellent adhesion properties;
- easy and simple application process;
- the material dries quickly;
- not afraid of engine oil and aggressive chemicals.
Advantages of epoxy primer:
- the floor formed durable glossy film which closes the pores of the concrete, but does not fill the voids in its structure;
- water resistance;
- resistance to the influence of different chemicals;
- the coating does not burn and is not subject to wear for a long time.

Epoxy primer is waterproof and durable
Review of the best colors for the floors made of concrete from popular and trusted manufacturers
Professionals prefer such brands as Tikkurila's "Tapping", "Colors" and "Elakor". Among them there are both domestic and foreign manufacturers.
Dye Teping P1155 composition is epoxy-based, characterized by high resistance to abrasion. Staining recommended under certain conditions: air humidity in the room should be no more than 90%, and temperature - in the range 10-20 ° C (optimum rate is 22 ° C). The coating is able to withstand a load up to 220 kg / cm², it exhibits resistance to moisture, lubricants and detergent.
To paint the floors in the room 37m², need about 20 kg of composition Teping P1155. Price epoxy paint for concrete floors of this mark is within 8000-8200 rubles. per set, consisting of a curing agent and base.
Especially popular among the professionals use paint for floors "Tikkurila." Composition Temafloor 150 manufactured according to the manufacturer, ideal for the treatment of surfaces of various types of concrete:
- fresh screeds;
- floors that were already in operation;
- previously painted surfaces.

Tikkurila Paint is popular due to high quality
The main feature of this dye is the absence of solvents in its composition. The coating is capable of withstanding exposure to high temperatures (70 ° C), so that the mixture can be used for interior and exterior. One liter of this compound is enough for high-quality staining 6-8 m². Flow rate depends on the number of layers to be deposited on the floor. polymer paint for concrete floors Price epoxy is about 750 rubles. for 1 liter.
Useful advice!To a film coating on the floor after painting composition Temafloor 150 was elastic, it is recommended to use a special hardener - Temafloor Flex.
Dye "Polimerstoun-1" is a polyurethane topcoat. Staining is recommended when the moisture content is not more than 4%, and the room temperature does not fall below 5 ° C. After drying, the coating may be operated in a wide temperature range - from -50 to +100 ° C. For staining 1m² requires about 400 g of material. paints price for concrete floor is about 3,500 rubles. per piece 7 kg.
These compounds - are not the only options that can be used for the treatment of concrete surfaces.

Paint "Polimerstoun-1" can be purchased for 3.5 thousand. rub. 7 liters
Overview epoxy paint for concrete floors "Epostoun"
"Epostoun" - a two-component water-epoxy enamel. Its pigmented base consists of epoxy resin and fillers of fine fraction. The polymerization process is initiated amine hardener. As part of the enamel no organic solvents, so that the producer could receive floor paint is odorless.
Scope "Epostoun" paint:
- construction projects of any type;
- medical institutions;
- educational institutions.
This type of dye is different environmental cleanliness. Due to high strength "Epostoun" can be used as protective coatings for concrete floors in workshops and garages. In addition, the composition exhibits a remarkable resistance to atmospheric agents, so there are no restrictions on its external application. You can use this paint on quite open areas.

Enamel "Epostoun" different environmental friendliness and lack of odor
"Epostoun" suitable for processing of fresh concrete screeds. By staining can begin about a week after potting. The main thing that the concrete humidity by the time reached 15%. This does not mean that the composition can not be used for the treatment of old surfaces. The temperature in the dyeing must be at least 5 ° C. Recommended layer thickness - up to 500 microns. The color scheme is limited to just one shade - matt gray.
Note! Dye "Epostoun" is not subject to tinting.
Overview polymer paint characteristics for the "Tex" floors
"Tex" - a dye made on the basis of PVC resins. This structure creates a coating on the treated surface with a matte effect, which is highly resistant to wear. This type of dye provides reliable protection of concrete floors from damage, and also the negative influence of rainfall. With the help of "Tex" composition can significantly prolong the service life of the concrete base.
Permitted coloring, when the outside temperature is below zero. For drying the composition takes a few hours. After the coating is hardened, the surface can be cleaned with detergents. The composition is able to withstand a short contact with oil, gasoline and alkalis. Paint "Tex" concrete floor can be used both outside and inside the premises.

Paints for concrete floors "Tex" are resistant to mechanical damage
dye advantages:
- simple and easy process of drawing;
- high protection of concrete floors against various negative factors;
- durability;
- matte coating.
Flow of the dye is 1 kg per 4-5 meters. To get a quality result of staining, the manufacturer recommends the use of a complex system, which consists of impregnation "Protex" and topcoat "Tex".
Table with paint prices for "Tex" sex:
The volume of the container, kg | price, rub. |
3 | 1030 |
10 | 3550 |
25 | 6250 |
Paint for concrete floor "Teksipol" acrylic-based
"Teksipol" is made on the basis of acrylic resins. As part of this dye has a organic solvent. This circumstance is largely affected the price of acrylic paint for concrete floors. On the other hand, the performance of the coating is much improved.
The film coating that is formed on the concrete surface after dyeing, is not afraid temperatures. The dye is not destroyed by most acids, alkalis and petroleum products (with the exception of concentrated alkali), as well as alcohols, freezing or cooling fluids.
Paint "Teksipol" for concrete floors can be used for treatment of concrete, asphalt surfaces and cement screeds. The coating protects the material against moisture, corrosive chemicals and abrasive loads. Manufacturers are developing "Teksipol" as a coating with wear-resistant properties for industrial buildings, shopping centers, warehouses and garages.

Mixture "Teksipol" suitable for the treatment of concrete, cement and asphalt
After staining, the surface becomes glossy. Consumers are three color options:
- beige;
- Gray;
- red-brown.
These colors are basic, but customers who carried out the order, the manufacturer is to meet and provides the ability to choose any RAL color. The dye spreads well and have plenty of hiding. The "Teksipol" consumed sparingly, if before that the floor surface has been carefully prepared.
Table "Teksipol" cost paint:
The volume of the container, kg | price, rub. |
3 | 1250 |
10 | 4000 |
20 | 5800 |
Important! Since the dye composition contains organic solvent, the material has a pungent odor. In the process of its application must use personal protective equipment. After the polymerization process terminates, odor disappears completely.
Benefits "Betoksil" acrylic paint for concrete
"Betoksil" represents a single component polymeric acrylic-based enamel. It is suitable for de-dusting of concrete surfaces in areas of industrial and domestic purposes. Using this dye can be processed floors, sand-cement screed, curb stone and brick.
The scope of application of the paint on the concrete "Betoksil" applies:
- warehouse premises on the destination;
- garage complexes;
- manufacturing enterprises.

Dyes "Betoksil" refers to a polymer with a single-component composition of enamels
The dye forms on a concrete surface and a durable tough coating which exhibits a high resistance to wear. The composition can withstand contact with oil, gasoline, various detergents, as well as fats. The coating is not afraid of rain and temperature extremes. It can be operated in a wide temperature range - -40 to +50 ° C.
Painting works can be carried out at low temperatures (-20 ° C). The surface must be completely dry and neobledeneloy. The composition has good adhesive properties, coating forms therefore excellent coupling with concrete. After staining, the surface becomes a matte sexes.
The dye has a limited color gamut comprising such shades:
- light gray (basic tone);
- white;
- dark grey;
- red-brown;
- yellow.
Table of prices on ink "Betoksil":
The volume of the container, kg | price, rub. |
5 | 1000 |
30 | 5550 |
How to paint the floors of concrete: Preparing the base and application technology
With the help of a two-component composition can be painted with old floors, has been in operation, as well as freshly poured screed. Depending on the state of preparation of the base algorithm can be different.
If you intend to freshly poured screed staining, you must wait five days to be cured concrete. During this time of the material to evaporate excess moisture, so it will be easier to handle. Five days after pouring the screed surface is polished using a tool called "helicopter". Grinding is necessary in order to get rid of the unstable upper layer. It is a frozen cement "milk." Furthermore, by grinding fine surface defects are removed, and open pores.
After that the floor is cleaned all the dust and debris. You can use a vacuum cleaner construction. Since: Fresh screed has a substantially flat surface, no need for repairing the substrate prior to staining.

Before painting, it is necessary to repair the floor, and close all the cracks and crevices
If the processing will be subject to the old concrete floor, you need to make sure that moisture the surface should not exceed 4%. Otherwise the adhesive properties deteriorate the dye and drying the coating after it starts to flake off.
Algorithm training the old floor staining:
- Moisture check using a special tool.
- Removal of unstable areas, various defects and loose areas.
- Elimination of impurities (paint residues, oil stains, traces of bitumen).
- Preparation cracks and crevices to zadelke (defect worked at a depth and a width of 8-10 mm).
- Garbage collection.
- The primer surface.
- Sealing of cracks and crevices using repair mortar or epoxy paint mixed with quartz sand.

Priming concrete floor - an important step prior to painting the surface
After repair the surface of the "patches" have to dry out. Before painting, they do not need further priming.
How to paint the concrete: The technology of drawing a two-component composition
Before you can use all the colors of the components must be thoroughly mixed. Fence mixture is carried out directly from a paint roller trays. You can pour a bit of structure to the floor and evenly distribute it using the same roller. If the concrete base carefully prepared and primed, it will not absorb the excess paint.
After drying the first layer on the concrete surface is formed rough coating, called "orange peel". The paint is desirable to apply at least two layers. This will improve the quality of decorative and protective properties of the coating. The second layer is applied after the first completely dry. This requires about 8 hours. Do not make too big a break between the layers, the pause should not last more than 24 hours. recommended roller to move in another direction, not to leave gaps in the secondary staining.

To create a high-quality paint coatings must be applied in at least two layers
After applying the topcoat must wait until the coating is completely dry and hardened. Many manufacturers are allowed to commission painted floors within a day. But do not be too hasty and abuse this recommendation. Surface coated with epoxy paint, will be ready for use within a week.
If the composition is chosen correctly, and its application was performed without disturbing the technology, such a coating will last a very long time, effectively performing its protective function.