Pour augmenter la durée de vie du moteur électrique, il est nécessaire d'effectuer des travaux de maintenance réguliers. Ils ne nécessitent pas de coûts élevés, mais prolongeront considérablement la durée de vie. La principale raison de la défaillance des machines électriques est l'augmentation de l'humidité des enroulements. En conséquence, une panne d'isolation se produit et, par conséquent, une défaillance de l'équipement. Pour éviter que cela ne se produise, il est nécessaire de mesurer régulièrement la résistance des enroulements. Il doit être conforme à la réglementation. Pour les moteurs électriques jusqu'à 400 kW, la résistance doit être d'au moins 10 mégohms. La mesure de la résistance doit être effectuée à une température de l'air normale avec une humidité normale. Mais si la température du moteur fonctionnait, la résistance devrait être d'au moins 3 mégohms et, avec une humidité de l'air accrue, d'au moins 0,5 mégohm. Ces indicateurs sont déterminés par GOST R 51689-2000 pour les moteurs électriques asynchrones. S'il y a des écarts dans les paramètres, l'enroulement doit être séché. Dans cet article, nous parlerons de la façon dont les moteurs électriques sont séchés et de ce qui est nécessaire pour cela.
Des méthodes courantes sont utilisées pour le séchage :
- chauffage extérieur;
- chauffage par pertes par induction;
- séchage en appliquant une tension réduite aux enroulements.
Considérons chacune des méthodes ci-dessus.
Teneur:
- Séchage du moteur avec chauffage externe
- Éliminer l'humidité avec des lampes à incandescence
- Méthode de perte d'induction
- Séchage des enroulements à tension réduite
- Autres méthodes
- Conclusion
Séchage du moteur avec chauffage externe
Tous les types de moteurs électriques sont séchés par chauffage externe. Et pour les machines électriques qui fonctionnent depuis longtemps dans des pièces très humides, c'est la seule option.
Habituellement, un appareil spécial est utilisé pour cela. C'est une armoire de séchage qui reçoit de l'air chauffé. La figure ci-dessous montre l'appareil dans lequel les moteurs électriques sont séchés.
Des éléments chauffants soufflés avec de l'air sont utilisés comme appareil de chauffage. La température dans le four est maintenue à 900AVEC.
Le moteur est démonté. Il manque des chapeaux de palier avant et arrière. Le rotor est démonté. Le flux d'air est dirigé de manière à ne pas entrer dans le bobinage. Ceci est fait pour éviter une surchauffe locale des fils.
Éliminer l'humidité avec des lampes à incandescence
En l'absence du dispositif décrit, le chauffage est effectué à l'aide de lampes à incandescence. Selon la puissance du moteur, des ampoules d'une puissance de 300 W à 1 kW sont utilisées. Pour cela, le moteur électrique est démonté, le rotor et les chapeaux avec roulements sont retirés. Les lampes sont placées à l'intérieur, montées sur un bouclier dans des supports en céramique.
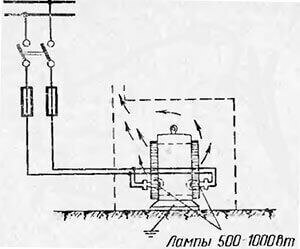
La figure ci-dessus montre le schéma de connexion des lampes à incandescence.
Les petits moteurs peuvent être séchés à l'extérieur à la maison. Dans ce cas, aucun appareil spécial n'est requis. Peut être séché dans un four ordinaire. Pour accélérer le processus, il est recommandé de prévoir un échange d'air.
Dans les ateliers de réparation de moteurs électriques, des fours à chambre pour le séchage et la cuisson des moteurs électriques PEK-01 sont utilisés. Ils maintiennent des températures jusqu'à 400°C.
Ils disposent d'une unité de contrôle programmable qui vous permet de programmer divers processus thermiques. Associé à la convection forcée, l'étuve de séchage vous permet de l'utiliser efficacement pour éliminer l'humidité par chauffage direct.
Méthode de perte d'induction
Pour sécher les moteurs électriques sans démontage, utilisez la méthode de perte d'induction. L'essence de la méthode est qu'un fil est enroulé sur le dessus du boîtier du moteur. Pour cela, des fils isolés sont utilisés. Le nombre de tours et la section sont calculés en fonction de la tension d'alimentation et de la puissance du moteur. Le moteur électrique est chauffé par la méthode de perte inductive.
S'il est censé sécher les enroulements par la méthode de la perte de chaleur, le moteur est alors démonté. Un enroulement est enroulé sur le stator, selon le principe d'un transformateur torique. L'avantage de cette méthode est la possibilité d'appliquer une tension monophasée de 220 volts. Cette méthode de chauffage nécessite de surveiller le courant dans les enroulements.
La figure ci-dessous montre un circuit de chauffage par induction et des méthodes d'enroulement de fil.
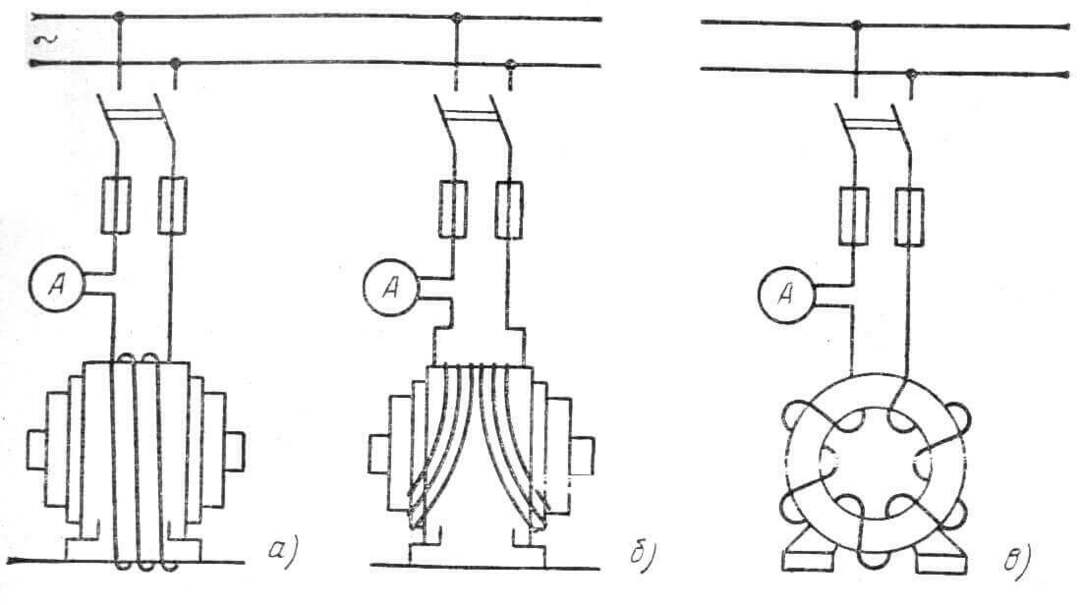
Séchage des enroulements à tension réduite
La méthode de séchage d'un moteur électrique à tension réduite est utilisée si la résistance d'isolement ne diffère pas beaucoup de la résistance nominale. Cela signifie que les enroulements ne sont pas saturés d'humidité.
Le démontage du moteur n'est pas nécessaire avant la mise en service. Dans les machines électriques avec un rotor à cage d'écureuil, le rotor est fixe contre la rotation. Et dans les machines à rotor de phase, les bagues collectrices sont court-circuitées entre elles.
Une sous-tension est appliquée aux enroulements. Pour cela, une ou deux machines à souder sont utilisées. Les transformateurs de soudage sont généralement utilisés. Le courant alternatif provoque un échauffement des enroulements. Dans ce cas, la surchauffe des enroulements ne se produit pas, car ils sont alimentés en tension de 0,08 à 0,17 du nominal.
Cela élimine la possibilité de surchauffe locale due à de faibles courants. Elles vont de 50 à 70 % des valeurs nominales.
Pendant le chauffage, le rotor est périodiquement libéré et tourné. Cela permet de ventiler le moteur et de raccourcir le temps de séchage. Pour exclure un chauffage inégal dans chaque enroulement, le courant est surveillé.
La figure ci-dessous montre le schéma de connexion des postes à souder.
Le chauffage des enroulements avec une tension continue est possible. Mais pour cela, dans les moteurs asynchrones, le début et la fin des bobinages doivent être sortis dans un boîtier sur son corps.
Afin d'éviter la rupture de l'isolation des enroulements, la fourniture et la suppression d'une tension constante ne s'effectuent que par l'intermédiaire d'un rhéostat.
Le moteur peut être séché de la même manière avec une tension alternative monophasée. Dans ce cas, la tension est appliquée à chaque enroulement séparément. La commutation s'effectue alternativement toutes les heures.
L'onduleur de soudage RESANTA SAI-160 peut être utilisé comme source d'alimentation. Mais pour limiter le courant, vous devrez choisir une résistance de limitation de courant.
La figure ci-dessous montre les schémas de connexion moteur asynchrone à une source de courant continu.
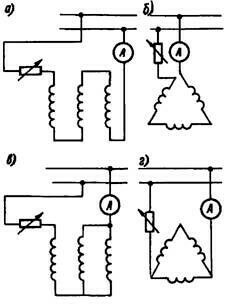
Autres méthodes
Pendant le fonctionnement, divers facteurs défavorables affectent les machines électriques. En conséquence, l'humidité s'accumule à l'intérieur, ce qui raccourcit leur durée de vie ou entraîne leur défaillance. Élimination de l'humidité, éventuellement par d'autres méthodes de séchage de l'isolation des enroulements des moteurs électriques.
Les lampes infrarouges sont utilisées pour éliminer l'humidité et accélérer le processus. Cette méthode est appelée méthode de thermoradiation. Les enroulements sont chauffés par des rayons infrarouges. En tant que source, des lampes spéciales avec un réflecteur miroir, des éléments tubulaires ou des panneaux métalliques sont utilisées, qui sont chauffées à 300-4500 AVEC.
Après chauffage, ils commencent à émettre des rayons infrarouges. Cette méthode est plus économique et efficace que la méthode de convection traditionnelle. Il est généralement utilisé après que le stator a été imprégné de vernis. Le procédé crée des conditions dans lesquelles le solvant est rapidement éliminé.
IMPORTANT! Les enroulements ne sont imprégnés qu'après séchage.
Habituellement, ils posent la question - à quelle puissance du moteur électrique l'isolation est séchée avec des lampes infrarouges. Les moteurs électriques de n'importe quelle puissance peuvent être chargés dans les caméras IR, mais il est conseillé d'utiliser la méthode pour les moteurs de grande puissance. Parce que ces caméras sont polyvalentes et de grande taille.
Pour éliminer l'humidité des moteurs électriques basse tension sans démontage ni démontage, l'industrie produit un dispositif de séchage électro-osmotique de l'isolation des moteurs électriques UELSI.
Il s'agit d'un dispositif pratique pour l'élimination non thermique de l'humidité des moteurs. Conçu pour fonctionner dans des conditions d'humidité élevée jusqu'à 100 % et de températures ambiantes de -50 à + 400 S., c'est-à-dire il peut être utilisé même dans des conditions de mine.
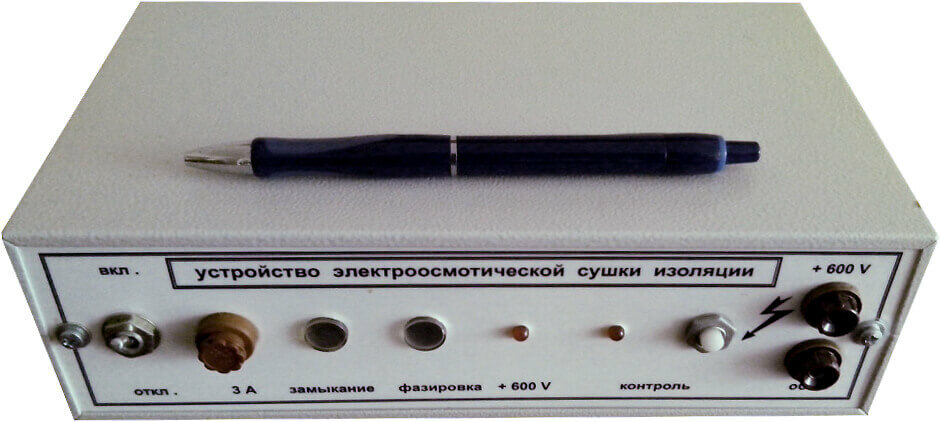
L'appareil génère des impulsions de courant de forme spéciale, sous l'influence desquelles se produit l'enroulement sous l'effet d'un transfert électro-osmotique de liquide dans les capillaires sous l'action d'un champ électrique.
Il est utilisé pour les tests accélérés et le contrôle de la qualité de l'isolation. L'utilisation de l'appareil n'entraîne pas de surchauffe locale, exclut la déformation et le vieillissement de l'isolation par échauffement, et augmente la ressource du moteur.
Conclusion
Après séchage ou réparation du moteur électrique, celui-ci est imprégné. Cette opération améliore la propriété isolante du revêtement du fil. Remplit l'espace entre eux. Cela empêche la poussière et la saleté de s'accumuler dans l'espace entre les spires.
Après démontage de la machine électrique, avant imprégnation, elle est soufflée à l'air comprimé. Ceci est nécessaire pour éliminer les pièces mécaniques et la poussière du bobinage. Imprégné de vernis ou de composé.
Pour ce faire, utilisez les méthodes suivantes :
- immersion du produit dans le vernis;
- irrigation par jets;
- sur les appareils avec alimentation en laque sous pression ;
- méthode d'injection sous vide;
- remplissage avec un composé.
Après imprégnation de vernis, le moteur est re-séché de l'une des manières. Désormais, les ateliers de réparation de moteurs électriques, afin de réduire leurs coûts, utilisent du vernis pour imprégner les bobinages des moteurs électriques à séchage à froid.