Content:
- Causes of occurrence
- Fault diagnosis
- How to identify a faulty winding
- Troubleshooting with a metal ball
- Checking with a special device
- Diagnostics of an anchor using a choke
- Measuring resistance with a tester
- Checking the stator with a tester
- Conclusion
Causes of occurrence
There may be several factors affecting the appearance of an interturn short circuit of an electric motor. Let's consider the main reasons why it occurs:
- The most common fault in which winding breakdown occurs is motor overload. It can occur when mechanical parts fail. For example, a rotor bearing is jammed, a malfunction has occurred in the conveyor, gearbox or other mechanism. As a result, an increased current flows through the windings, which leads to overheating of the wires and destruction of the insulation. A short circuit (SC) occurs between the turns.
- During the manufacture at the plant, a defect was allowed. This does not happen often, but it is possible. The insulation cracks during operation. The winding is damaged, an interturn short circuit occurs.
- During the repair, the technological process was disrupted. The winding is very tight. During operation, the electric motor heats up, the turns expand. Due to the tightly wound electrical winding, expansion is not possible. The varnish on the wires is damaged, an inter-turn circuit occurs.
- Improper storage will allow water to enter the motor, which can lead to insulation breakdown.
With such a malfunction, the electric motor will not be able to work for a long time. Further heating of the winding will take place. The consequences of such a malfunction lead to engine failure. Therefore, it is important to identify the malfunction in time and take measures to eliminate it.
Fault diagnosis
The main symptom of an interturn short circuit is uneven heating of the case. This is due to the increased current consumption of one (faulty) winding. If overheating of one part of the housing occurs, then the motor must be de-energized and diagnosed.
It is performed as follows:
- Check the voltage on all windings. It should be the same, i.e. the network must be absent phase imbalance. After that, the currents in each winding are measured. Measurements are made current clamp. If the current in one winding differs from the others in a larger direction, then this indicates the presence of a malfunction in this winding.
- Using a high-precision ohmmeter, the resistance of the windings is measured. The values must be the same. It is impossible to check the presence of a short circuit with a conventional device. Because with a short circuit of only two turns, the resistance will change slightly.
- The short circuit to the case is determined using a megohmmeter. To do this, one end is connected to the body, and the other is connected to the windings in turn. Thus, the integrity of the insulation resistance is checked. Ideally, it should be the same on each winding or have slight deviations. It should be borne in mind that it changes depending on the temperature of the conductors.
The figure below shows a table of the dependence of the change in insulation resistance on temperature:
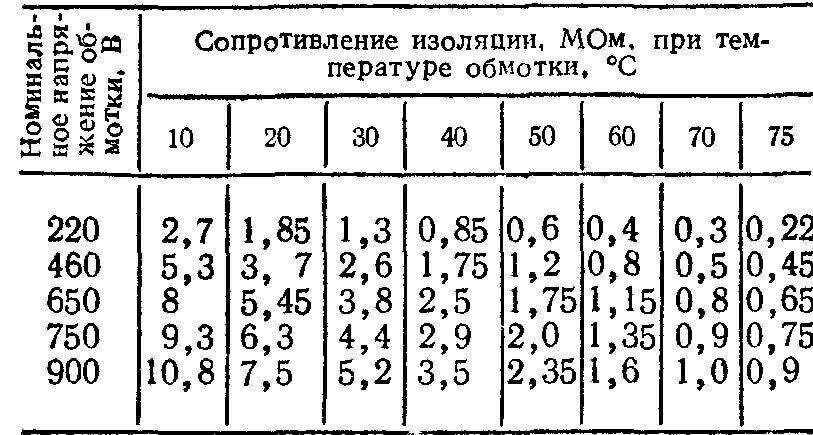
How to identify a faulty winding
To determine the turn-to-turn circuit in the electric motor, it must be disassembled. Carry out a visual inspection. The defect can be identified by the appearance of the windings. They show the places of meek circuit, as shown in the figure below for the malfunction of the rotor and stator:
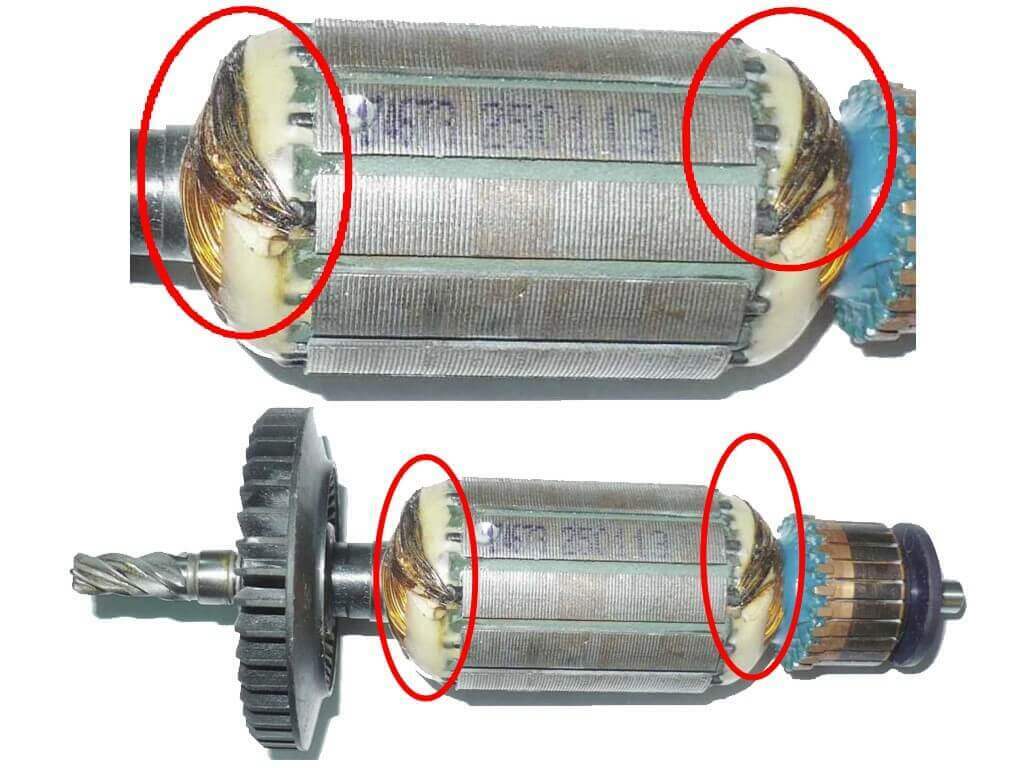
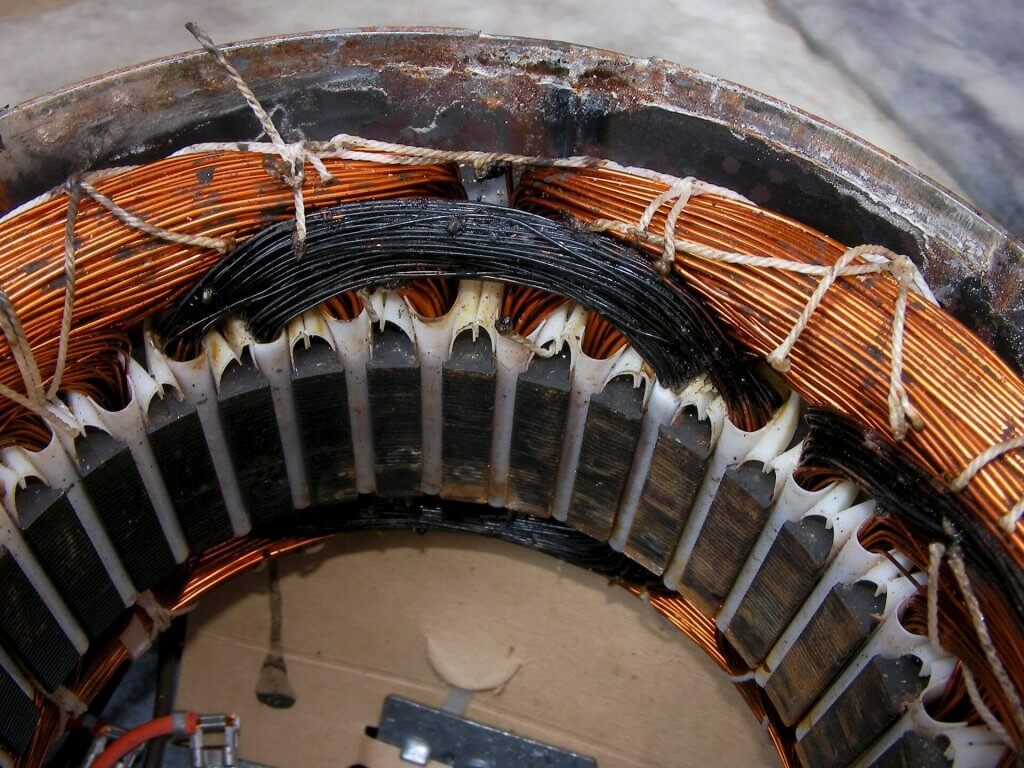
However, it is often impossible to visually detect signs of turn-to-turn closure. Therefore, the service personnel must know what to do in such situations. In the absence of visible faults, the following methods are used.
Troubleshooting with a metal ball
It is possible to identify a short circuit in the insulation using a three-phase step-down transformer. The secondary voltage must not exceed 40 volts.
The disassembled motor is energized from a transformer. A metal ball is launched in a circle inside the engine. If the windings are in good condition, it starts to "run" in a circle without stopping.
If there is a short circuit of the winding, then the ball, having made two or three circles, is magnetized at the place of failure.
If the ball is missing, you can check with a transformer iron plate. You can use iron from a faulty transformer. The plate is applied in a circle alternately. In the wrong place, the plate will begin to vibrate. In other places, it is magnetized.
When checking the serviceability of the electric motor, do not forget about safety precautions. The motor housing must be grounded. At the same time, it is strictly forbidden to apply voltage above 40 Volts to the windings.
The figure below shows the ball test method:
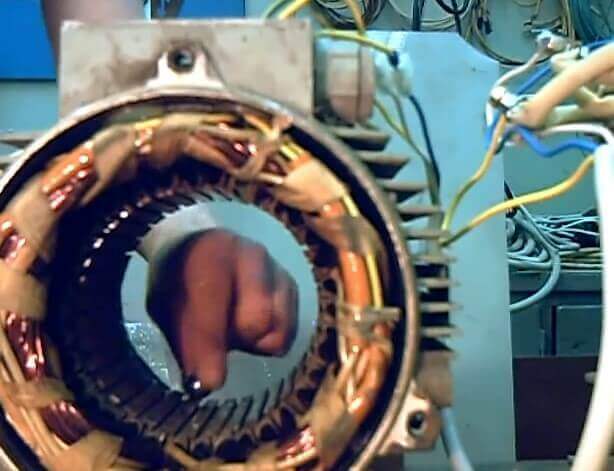
Checking with a special device
The search for the turn-to-turn short circuit of the electric motor can be performed using a device for testing the insulation breakdown of the windings. You can buy it online or make it yourself. Numerous schemes are shown on the Internet. They are not complicated. Any specialist who has skills in working with a soldering iron and who understands electrical circuits can repeat it.
How to determine the malfunction is described in detail in the instructions for the device. Diagnostics is performed in minutes. However, an oscilloscope is required to perform diagnostics.
This is an expensive device. Not all masters know how to work on it. Therefore, this verification method has not received mass distribution.
The industry is now producing devices that do not require an oscilloscope. It has two LEDs that indicate a malfunction.
The device is a generator, the oscillating circuit of which consists of a capacitor and a motor winding. A trimmer resistor is used to excite the circuit. In this case, the LED starts flashing. All windings are connected in turn. When a faulty winding is connected, the LED will be on continuously. Those. there will be a breakdown in generation.
Diagnostics of an anchor using a choke
A choke is used to check the armature. It is a cut-core transformer. A factory-made or home-made device is used.
It can be done in the presence of faulty vibration pumps "Kid" or "Trickle". Detailed instructions with a description are available on the Internet.
Measurements were carried out on a factory device and a home-made one, made according to the method described on the Internet. The result was the same.
How to check for malfunction with this device. An anchor fits into the cutout. The choke is energized. In this case, the armature winding will represent the secondary winding of the transformer.
Using a plate of transformer iron, we check the health of the winding. Gradually turning the armature, at the place of breakdown, the plate is magnetized to the armature and begins to vibrate. This is shown in the figure below:
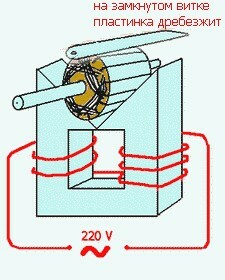
Measuring resistance with a tester
In the absence of a choke, you can check with an analog tester. It is worth noting that in this way it is possible to check the winding breakage, and the closure of the turns is checked as described above.
For this, measurements are made between the anchor lamellas. The resistance of the conductors must be the same.
Be sure to check the short circuit of the wires to the case. To do this, connect one end of the tester to the body and ring each winding in turn. This check is performed provided that there is no breakage in the windings.
The photo below shows how to measure the resistance of conductors:
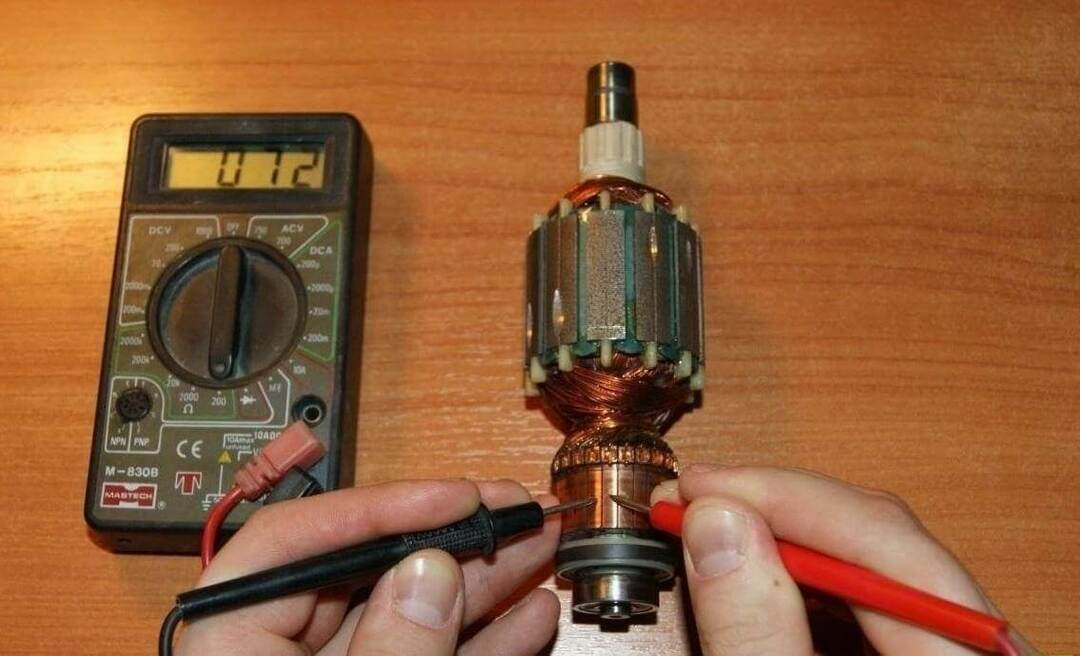
Checking the stator with a tester
You can check the integrity of the stator winding using a tester. To do this, it is enough to measure the resistance of each separately. Measurements are performed using a high-precision instrument. It is not superfluous to check for insulation breakdown on the case using a megohmmeter.
The figure above shows the continuity of the windings:
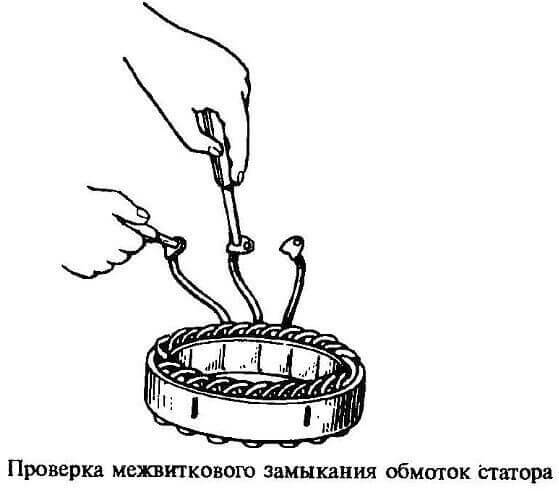
Conclusion
During operation, it is rather difficult to determine the turn-to-turn closure of the motor windings. Yes, and it does not occur often. Usually, engines with such a defect work until the last moment. Until smoke comes out of it.
Therefore, the service personnel does not have a question of how to eliminate the malfunction. The engine is rewound. They do the same with timely detection of a short circuit in the windings, rewind the faulty part. It should be borne in mind that it is impossible to eliminate the closure of the turns with each other without rewinding.