To increase the service life of the electric motor, it is necessary to carry out regular maintenance work. They do not require high costs, but will significantly extend the service life. The main reason for the failure of electrical machines is the increased humidity of the windings. As a result, insulation breakdown occurs, and as a result, equipment failure. To prevent this from happening, it is necessary to regularly measure the resistance of the windings. It must comply with the regulations. For electric motors up to 400 kW, the resistance must be at least 10 megohms. Resistance measurement should be carried out at normal air temperature with normal humidity. But if the engine temperature was operating, then the resistance should be at least 3 megohms, and with increased air humidity, at least 0.5 megohms. These indicators are determined by GOST R 51689-2000 for asynchronous electric motors. If there are deviations in the parameters, then the winding should be dried. In this article, we will talk about how the drying of electric motors is performed and what is needed for this.
Common methods are used for drying:
- external heating;
- heating using induction losses;
- drying by applying reduced voltage to the windings.
Let's consider each of the above methods.
Content:
- Drying the engine with external heating
- Removing moisture with incandescent lamps
- Induction loss method
- Drying of windings with reduced voltage
- other methods
- Conclusion
Drying the engine with external heating
All types of electric motors are dried using external heating. And for electric machines that have been working in rooms with high humidity for a long time, it is the only option.
Usually a special device is used for this. It is a drying cabinet that receives heated air. The figure below shows the device in which the electric motors are dried.
Heating elements blown with air are used as a heater. The temperature in the oven is maintained at 900WITH.
The engine is disassembled. It lacks front and rear bearing caps. The rotor is dismantled. The air flow is directed so that it does not enter the winding. This is done to prevent local overheating of the wires.
Removing moisture with incandescent lamps
In the absence of the described device, heating is carried out using incandescent lamps. Depending on the power of the engine, light bulbs with a power of 300 W to 1 kW are used. For this, the electric motor is disassembled, the rotor and caps with bearings are removed. Lamps are placed inside, mounted on a shield in ceramic holders.
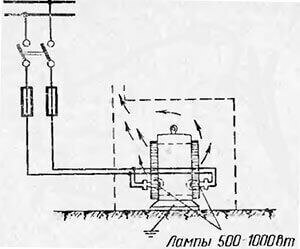
The figure above shows the connection diagram for incandescent lamps.
Small motors can be dried externally at home. In this case, no special devices are required. Can be dried in an ordinary oven. To speed up the process, it is recommended to provide air exchange.
In workshops that are engaged in the repair of electric motors, chamber furnaces for drying and firing of PEK-01 electric motors are used. They maintain temperatures up to 400 ° C.
They have a programmable control unit that allows you to program various thermal processes. Together with forced convection, the drying oven allows you to effectively use it to remove moisture by direct heating.
Induction loss method
To dry electric motors without disassembly, the induction loss method is used. The essence of the method is that a wire is wound on top of the motor housing. For this, insulated wires are used. The number of turns and the cross-section are calculated depending on the supply voltage and motor power. Heating of the electric motor is carried out by the inductive loss method.
If it is supposed to dry the windings by the method of heat loss, then the motor is disassembled. A winding is wound on the stator, according to the principle of a toroidal transformer. The advantage of this method is the ability to apply a single-phase voltage of 220 volts. This heating method requires monitoring the current in the windings.
The figure below shows the induction heating circuit and conductor winding methods.
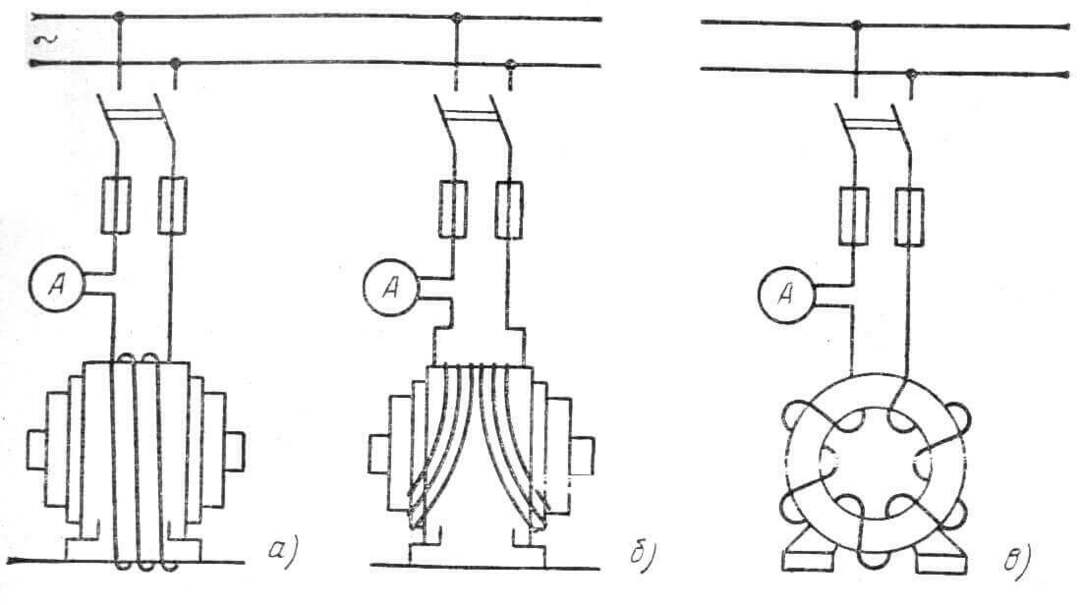
Drying of windings with reduced voltage
The method of drying an electric motor with reduced voltage is resorted to if the insulation resistance does not differ much from the nominal one. This means that the windings are not saturated with moisture.
Disassembly of the motor is not required prior to operation. In electric machines with a squirrel-cage rotor, the rotor is fixed against turning. And in machines with a phase rotor, slip rings are short-circuited among themselves.
An undervoltage is applied to the windings. For this, one or two welding machines are used. Welding transformers are usually used. The alternating current causes the windings to heat up. In this case, overheating of the windings does not occur, because they are supplied with voltage from 0.08 to 0.17 of the nominal.
This eliminates the possibility of local overheating due to low currents. They range from 50 to 70% of the nominal values.
In the process of heating, the rotor is periodically released and rotated. This ensures ventilation of the motor and shortens the drying time. To exclude uneven heating in each winding, the current is monitored.
The figure below shows the connection diagram of the welding machines.
Heating of the windings with DC voltage is possible. But for this, in asynchronous motors, the beginning and end of the windings must be brought out into a box on its body.
In order to avoid breakdown of the insulation of the windings, the supply and removal of a constant voltage is carried out only through a rheostat.
The motor can be dried in the same way with single-phase alternating voltage. In this case, voltage is applied to each winding separately. Switching is carried out alternately every hour.
The RESANTA SAI-160 welding inverter can be used as a power source. But to limit the current, you will have to choose a current-limiting resistance.
The figure below shows the connection diagrams asynchronous motor to a direct current source.
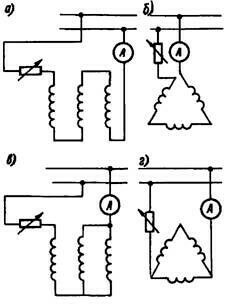
other methods
During operation, various adverse factors affect electrical machines. As a result, moisture accumulates inside, which shortens their service life or leads to their failure. Removing moisture, possibly by other methods of drying the insulation of the windings of electric motors.
Infrared lamps are used to remove moisture and speed up the process. This method is called the thermoradiation method. The windings are heated by infrared rays. As a source, special lamps with a mirror reflector, tubular elements or metal panels are used, which are heated to 300-4500 WITH.
After heating, they begin to emit infrared rays. This method is more economical and efficient than the traditional convection method. It is usually used after the stator has been impregnated with varnishes. The method creates conditions under which the solvent is rapidly removed.
IMPORTANT! The windings are impregnated only after drying.
Usually they ask the question - at what power of the electric motor the insulation is dried with infrared lamps. Electric motors of any power can be loaded into IR cameras, but the method is advisable to use for high-power motors. Because such cameras are versatile and large in size.
To remove moisture from low-voltage electric motors without disassembly and dismantling, the industry produces a device for electroosmotic drying of the insulation of electric motors UELSI.
This is a convenient device for non-thermal removal of moisture from engines. Designed for operation in conditions of high humidity up to 100% and ambient temperatures from -50 to + 400 S., i.e. it can be used even in mine conditions.
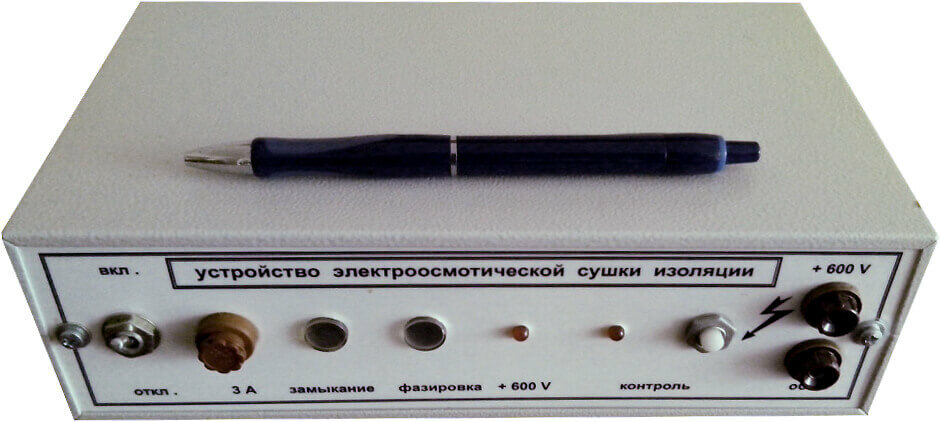
The device generates current pulses of a special shape, under the influence of which the winding produces the effect of electroosmotic transfer of liquid in the capillaries under the action of an electric field.
It is used for accelerated testing and quality control of insulation. The use of the device does not lead to local overheating, excludes deformation and aging of the insulation from heating, and increases the engine resource.
Conclusion
After drying or repairing the electric motor, it is impregnated. This operation improves the insulating property of the wire coating. Fills in the space between them. This prevents dust and dirt from accumulating in the inter-turn space.
After disassembling the electric machine, before impregnation, it is blown with compressed air. This is necessary to remove mechanical parts and dust from the winding. Impregnated with varnish or compound.
To do this, use the following methods:
- immersing the product in varnish;
- jet irrigation;
- on devices with under pressure lacquer supply;
- vacuum injection method;
- filling with a compound.
After impregnation with varnish, the engine is re-dried in one of the ways. Now, electric motor repair shops, in order to reduce their costs, use varnish to impregnate the windings of cold-drying electric motors.