The author of the article: Ph.D. G.A. Bershidsky
Until the end of the last century, cast iron radiators were the main heating devices in Russia. Then came convectors based on thick-walled steel pipes and steel panel radiators. Other materials for the production of heating devices were practically not used. Currently, steel pipelines, boilers, heating devices, etc. are still widely used. Therefore, the main characteristics of network water for heat supply systems are focused on the use of steel. These characteristics are regulated by the "Rules for the Technical Operation of Power Plants and Networks of the Russian Federation", according to which the value pH of acidity pH of network water should be in the range of 8.3-9.5 for closed heat supply systems and 8.3-9.0 for open systems. The dissolved oxygen content should not exceed 20 μg / l.
Aluminum has long attracted the attention of developers of heating equipment due to its unique properties, such as high thermal conductivity, lightness, plasticity, the ability to manufacture heating devices by injection molding and extrusion. The combination of these properties makes it possible to obtain devices that are distinguished by high heat transfer, high-quality outer surface and aesthetic appearance, corresponding to modern interiors. High thermal conductivity, 5 times higher than the thermal conductivity of steel, combined with a low density of aluminum (3 times lighter than steel), make it possible to obtain a lightweight radiator with efficient fins.
However, two significant drawbacks sharply limit the scope of application of aluminum radiators. Firstly, cast aluminum radiators turned out to be quite fragile, which led to accidents, especially when the tenants were unauthorizedly replaced by more robust design heating devices (usually steel convectors or cast iron radiators) to visually attractive aluminum radiators. Subsequently, this drawback was overcome: now aluminum radiators are produced that can withstand the pressure of the coolant, much exceeding the possible working pressure in heating systems by optimizing the configuration of the column cross-section and increasing their thickness walls.
The second drawback is the increased exactingness of aluminum radiators to the quality of the coolant - to be overcome for now fails: attempts to apply various protective coatings to the inner surface cannot be fully recognized successful. The resistance of aluminum and its alloys to corrosion is determined by the presence or absence on the inner surface of a dense film consisting of aluminum oxide Al2O3. This film has an amphoteric character, that is, it dissolves in both alkaline and acidic media. Figure 1 shows the dependence of the corrosion rate of aluminum on pH, given in the book by T.M. Petrova, V.N. Voronov and B.M. Larina "Technology and organization of the water-chemical regime of nuclear power plants", M., 2012. The figure shows that this curve has a pronounced minimum. With an increase in pH from 8.5 to 9.5, the corrosion rate of aluminum increases by an order of magnitude (from 0.1 to 1 g / (m2h)). The same happens when the pH decreases from 6.5 to 4.2, but there are practically no such pH values in the heating water supply systems.
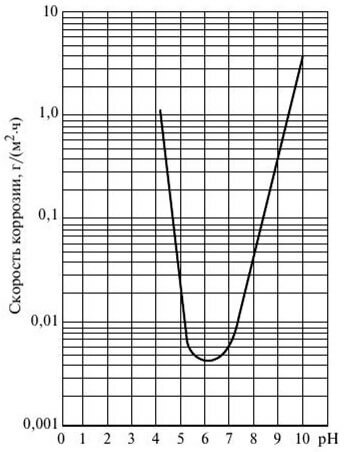
Dependence of the corrosion rate of aluminum on the pH of the medium.
Thus, the dense protective oxide film successfully resists corrosion in the pH range from 6.5 to 8.5. At pH values outside this range, the oxide film breaks down, and corrosion penetrates to a great depth of the wall, causing even through holes. In this case, as a rule, small leaks appear first. Note that if corrosion has not yet led to a loss of radiator tightness, a decrease in wall thickness leads to a gradual decrease in its strength and, consequently, to accidents due to even a slight increase pressure. Such accidents can be catastrophic, since a section weakened by corrosion usually ruptures along the entire height of the column, and water floods the rooms of the underlying floors.
In this regard, it was quite natural that the idea appeared to combine aluminum and steel in one structure in order to use their advantages. In general, bimetals are widely used in various fields of technology. Usually one layer is made of inexpensive steel, and the other is made of non-ferrous metals, in this case aluminum. The first bimetallic radiators appeared in Europe in the middle of the last century. Only vertical columns were bimetallic in such radiators: steel pipes were placed in the injection mold for the passage of the coolant. In horizontal collectors, the coolant was in direct contact with aluminum.
Such hybrid radiators (the common term is "semi-metallic") are still being produced, although it cannot be considered logical a design in which a coolant with pH = 8.3-9.5 is required for one part of the radiator (column), and for the other (collectors) - 6,5-8,5. This means that "semi-metallic" radiators can work normally only in a narrow pH range from 8.3 to 8.5. This excludes the possibility of their use in the most common in Russia heating systems with dependent connection to heating networks, equipped with make-up water treatment systems.
Based on the foregoing, "semi-metallic" radiators should be attributed not to bimetallic, but to aluminum radiators. To confirm or refute this proposal, it is necessary to conduct tests to determine the corrosion rate when the pH of the coolant changes over a wide range.
In addition, the thermal expansion coefficient of aluminum is twice that of steel. Because of this, when the temperature of the coolant changes, a tension arises between the steel tube and the aluminum fins of the column. The mutual displacement of these layers leads to loosening of the contact between them, to an increase in the thermal resistance of the contact and, consequently, to a decrease in the heat transfer of such radiators during operation. To assess this reduction, an accelerated performance test should be carried out by alternately passing 20 ° C water through the radiator.0C and 900C (at least 250 cycles) and comparing its heat flux before and after this "buildup".
Currently, improved bimetallic radiators, the embedded parts of which are a welded H-shaped structure of steel pipes, are deservedly in the greatest demand. Thus, the horizontal and vertical channels are made of steel, and the contact of aluminum with water is excluded. Such radiators behave like steel and can be used in conventional systems at normalized pH values = 8.3-9.5. They have increased strength, therefore, when using them, accidents associated with exceeding the permissible pressure, including hydraulic shocks, are practically excluded.
It should be noted that although bimetallic radiators are heavier than aluminum and "semi-bimetallic" ones, the consumption of aluminum alloy is minimal here, since only thin-walled fins are made of it.
It is possible to distinguish bimetallic radiators from "semi-bimetallic" ones by means of a magnet applied to the connecting holes.
conclusions
- Bimetallic radiators, in which the contact of the coolant with aluminum is excluded, can be used in almost any water heating systems.
- Aluminum, including "semi-metal" radiators, can be used in heating systems with independent connection to heating networks and in individual systems with a permanent coolant.
Useful video on the topic: